What kind of impact could increased efficiency have on your farm? What if you could solve your labor concerns and gain milk production with less human hours? Our customers have gained production and enhanced their quality of life with the help of our dedicated team of professionals. Learn more about their projects here.
Same barn, new technology
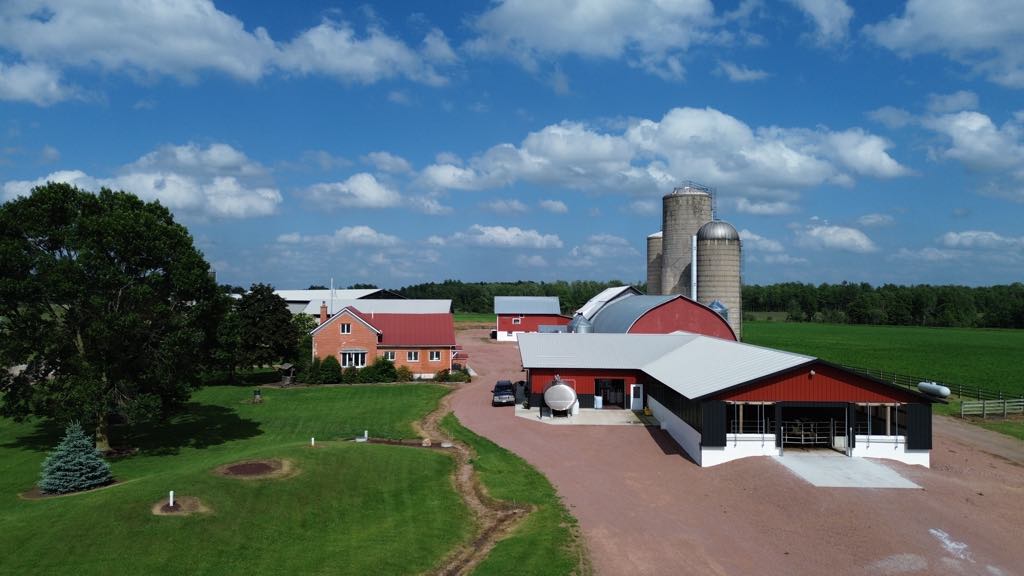
Ninnemann Enterprises
The Ninnemann Family
For the Ninnemann family, seeing was believing when it came to upgrading the farm with robotic equipment. The family was always intrigued with robots, but thought they would have to build a whole new barn to make it work on their farm. They did not want to do that because their barn had served them well for five generations.
Ninnemann Enterprises is owned and operated by Alex, Aaron, Adam, Herb and Fred Ninnemann. The family milks 120 cows.
The family had always milked in a tie-stall set-up. They were getting worn out, and Aaron expressed desire to run the farm with robots while maintaining his full time job. They decided to get serious about researching robots.
They started with a Google search of Lely dealerships near them, which led them to Seehafer Refrigeration. After talking with the owner, John Seehafer, the family realized that they could upgrade while utilizing the original barn. John took the Ninnemanns on a tour of a farm that had retrofitted their tie-stall to accommodate robots.
“We came back and told Herb it’s really simple, a piece of cake,” Adam said. “So, we went back the next day and that was the last of the looking we did. A month later, we signed the paper work.”
Within that month, the family discovered all that robotic farming had to offer. They added a Juno feed pusher and a Lely Walkway footbath to the upgrade, as well as the two milking robots.
“The more technology we discovered, the more sense it made,” Adam said. “Everybody we talked to said they didn’t run a foot bath because it was difficult, so the Lely Footbath solved that. And the feed pusher was a no-brainer because we are pushing a lot of feed in a small area so we’re not pushing that by hand.”
The family said that working with the crew at Seehafer Refrigeration has been impressive, from touring options with John and right through the installation and start up process, which involved five days of on-farm support from the dealership.
“I believe Seehafer understands the business better than anyone,” Aaron said. “They’re not here just to install equipment. They are getting you up and running and getting you comfortable with everything that has to happen.”
After the initial start up, continuing support is offered through route service, on-call technical support and their Farm Management Support person, Jackie Plank.
“I feel like Jackie is always a phone call away,” Aaron said. “I don’t ever feel like I’m left out.”
The technology has allowed more people to be involved and flexible within the operation. Everyone is cross trained, which makes it easy for them to rotate taking time away.
“It’s made farming fun again,” Adam said.
The flexibility has allowed Aaron to be more active on social media as well. He shared the farm’s transition story as a way to educate others who may have been thinking about an upgrade and might have had the same concerns he did.
“I did it to show other farmers to use what you got,” Aaron said. “Put in one robot or two or whatever it is to keep the family farm going. Just because you’re adding technology doesn’t mean you need to add a thousand cows.”
Renewing their dream of dairy
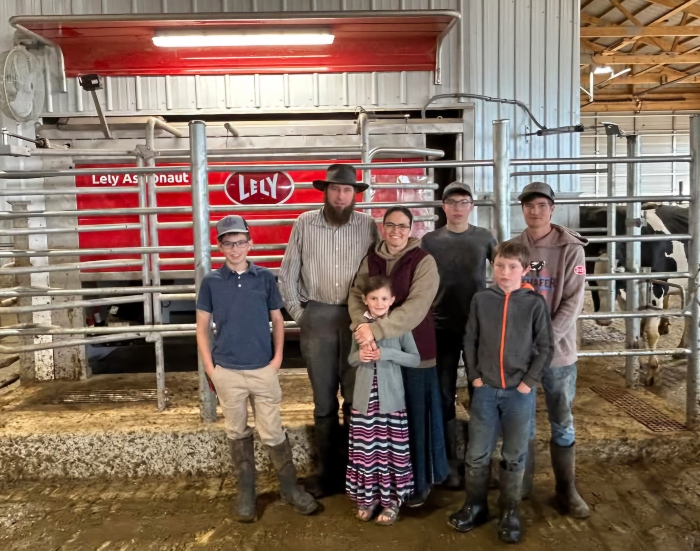
High View Holsteins
The Knaus Family
Brent Knaus always dreamed of having his own farm. When Brent and his wife Lucy Anne were young newlyweds, that dream became reality when they took over the dairy farm across from where Brent’s family farmed. Now 23 years later, the Knaus family has upgraded to three Lely A5 robotic milkers with the help of Seehafer Refrigeration- Sparta. Brent said it has renewed his dream of dairy farming.
“I kind of feel like I got my farm back,” Brent said. “Before, everything revolved around the hired help and now we can do whatever, just the boys and me.”
Brent and Lucy Anne milk 190 cows with their children Landon, Shane, Regan, Evan, Aden and Jan. Landon and Regan are full time on the farm.
When they first started out, Brent and Lucy Anne milked in the original 35-stall stanchion barn which they used as a flat parlor. As their herd grew, they built a freestall barn to house the cows. Eventually they were milking 190 cows in the original barn and chores took six hours per milking. Brent thought they would milk in the original barn for a few years and then upgrade to a parlor. However, they could not find a building plan to work without adding 100 cows, which they were not interested in.
Their aging facility was no longer going to pass inspection, and the couple knew they needed to either upgrade or sell out. Lucy Anne said options were dwindling. Eventually, Brent and Lucy Anne began to consider changing their focus from a parlor to robots.
“Our doors had all closed and we were looking for a door to open,” Lucy Anne said. “This was very big and very new, but all of a sudden these doors were opening and we knew this is the way it was supposed to be.”
Once they decided to go the robotic route, everything seemed to fall into place, the Knaus family said. From the bank approval to the robot delivery and even construction, the transition process was relatively smooth.
“The whole process and the whole building experience was just so good,” Brent said. “I was very impressed how they (Seehafer Refrigeration) set me up with spare parts and taught me how to identify and fix problems. That was great.”
Lucy Anne agreed.
“They took care of all of the unknowns for us,” Lucy Anne said. “Alleck prepared us for so much.”
The robots are powered with the use of Starlink, a satellite internet provider, and a slave computer. There is no way to access the internet from the set up, but it enables the use of the robots. The system works with the family’s preferred flip phones to receive calls from the robots.
Lucy Anne said she has noticed a happy change in Brent since making the upgrade.
“There were days before we built this that I was like, this is your dream? Because he wasn’t happy,” Lucy Anne said. “He was overworked, stressed and burned out. But I’ve had no questions since August; he is living his dream.”
Brent agreed.
“I know dairy farming is not the most profitable thing, but it’s what I love doing,” Brent said. “Maybe I could do something else that would make more money, but if you aren’t happy, what good would that do?”
Robots solve labor, expansion issues

Hockerman Bros. Dairy
Back to managing cows
The Hockerman family is enjoying a more relaxed and efficient way of dairying since transitioning to robotic milking in 2022. Brothers Greg, Tom and Jason Hockerman milk 700 cows with the help of their dad, Bud, and Greg’s wife Dawn. The family transitioned to 12 Lely A5 robots and two Juno feed pushers in December 2022. The upgrade was the result of an expansion that took place in 2018, when they grew the herd from 350 to 700 cows.
Before expanding, they were milking in a double-10 herringbone parlor that was almost 50 years old.
“We went from milking around the clock three times a day with 350 cows to just getting through two times a day with 700 cows,” Greg said.
The brothers thought they would upgrade to a rotary parlor, but size and efficiency issues were not making that possible. They turned to robots instead.
The family decided on Lely A5 robots because they were already working with a Lely dealer to service their parlor, and because of what they saw when touring various farms.
“It was very interesting to see the attitudes of the guys with Lely robots compared to the other brands,” Greg said. “The ones with Lelys seemed more relaxed. It was just smooth.”
Since making the transition, the herd has increased their average daily production to 95 pounds per cow per day, on a weekly average. This is compared to an average of 82 pounds per cow when milking twice a day in the parlor.
“The robots took care of all our issues in the milking facility,” Greg Hockerman said. “We needed to cut down on labor and we needed to find some way forward that we could increase production.”
The milking robots solved a big labor problem for the Hockerman family, and the calls from the robots are less disruptive than the calls from the employees used to be.
“You’re still tied to the phone, but getting phone calls now, it’s giving me where I go and what to look for,” Greg said.
The data obtained from the monitoring system has allowed the Hockermans to improve their reproduction program as well. Prior to the Lely monitoring system, the family defaulted to hormone injections to achieve pregnancies. Now, 80% of pregnancies are bred on heat detection alone, including first service heifers.
“It was a big change for me in the way I managed both cows and people,” Greg said. “My wife has told me I’ve become a totally different person because I’m back to dealing with cows, which is what I want to do.”
Equipment Reliability
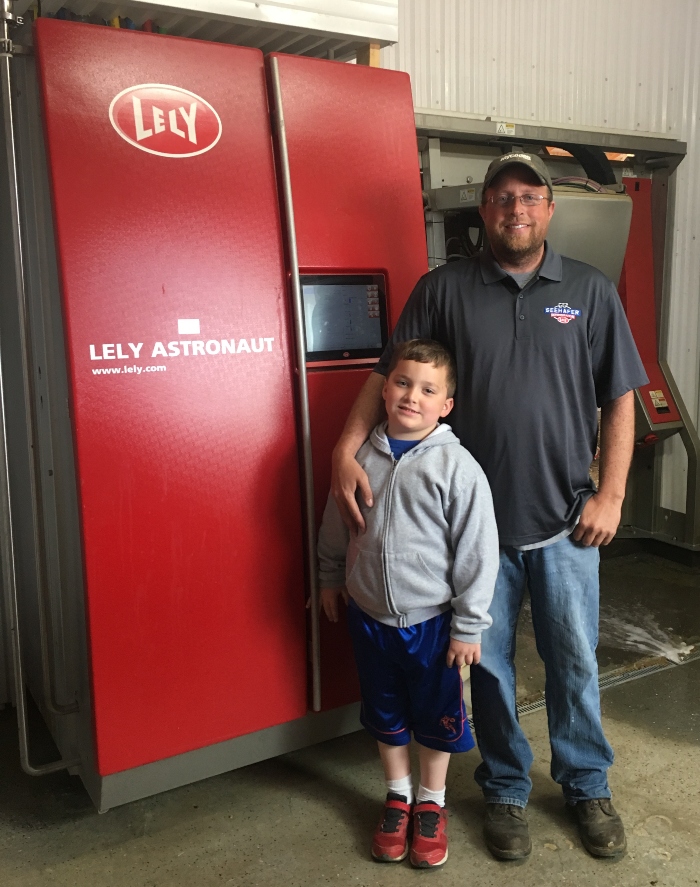
Josh Willson
Empire Dairy, LLC
Josh Willson is the owner of Empire Dairy LLC, which is home to three Astronaut A4 milking robots, 3 Luna brushes, and a Juno 100. They have all been running since January 2018. Before robots, Josh milked in a tie stall barn twice a day that is located right below his new facility. Not only is he the owner of his farm, but he also does nutrition work for other farmers.
“When making the choice to build a parlor or robots, the factors that led me to my decision was the availability in land and labor with cattle and employees. Someday, I’d like to have 600 cows milked by all robots. The general install of the robots was excellent, I don’t know how Seehafer’s could have done any better. The reliability of the equipment with robots is what really pushed me to robots; the equipment rarely fails. The service maintenance is easy to schedule and I have no significant downtime. The reliability of the system is second to none. After installing robots, we have half the labor and increases in production. The style of labor has shifted into more management practices to lead to the future. All the data points that come with this automation allow us to be more intense and precise with cow touches. We have learned to keep everything well maintained; the sand can be hard on equipment but we have learned what needs to be washed out everyday and kept with. We try to keep everything as clean as possible to further longevity. As far as the tags, robots, and Juno, they all work well together and complement each other. I wouldn’t want to operate without all of them working together. With the service from Seehafer’s, you won’t be dissatisfied. When there is a service call for the equipment, you don’t need a second service call to fix the first one.”
Quality Maintenance
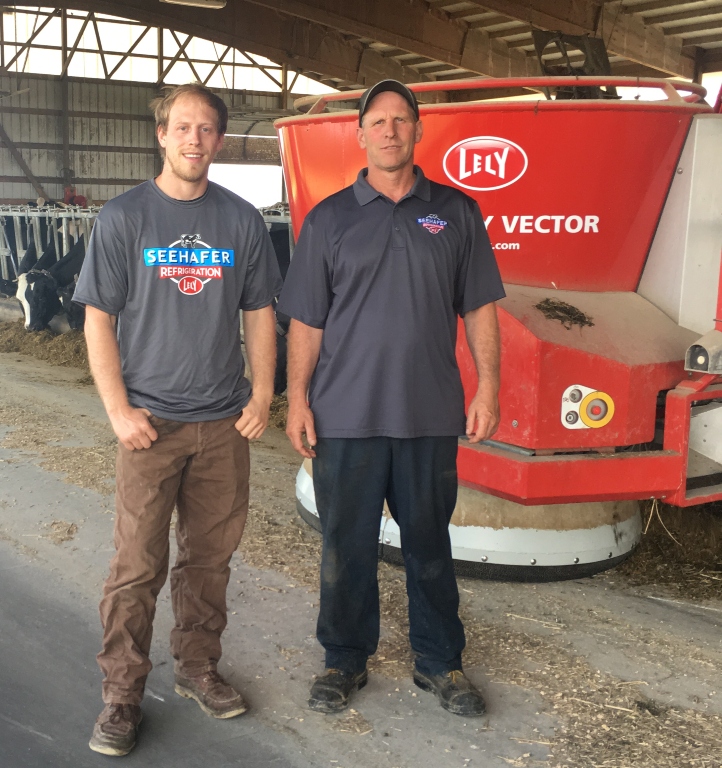
Mitch & Max Malm family
Mitch, Max, and the rest of the Malm family live in Loyal on the family’s 115-dairy cow farm. They have two Astronaut A4 milking robots that were started up in October of 2012 with 80 Holstein cows. They also have one Vector feeding system for the last six months.
“We put milking robots in 6 years ago to help with labor and making chores easier. We used to have 2-3 people doing chores morning and night in the tie stall barn and now we can do everything with one guy. The robots have made chores easier and have provided better production. We are now able to form our chores around when it works for us. If we are in the fields or with family, we can either do chores before we leave or when we get back and don’t have to stress about how well they are getting done while we are gone. We also get faster and useable data on the cows so we can be proactive verses reactive with the cows. The cows adapt to the system quicker than in the tie stall barn. They can take care of themselves and don’t need as much of our help. They like to be left alone and we feel robots made our cows calmer.
We started the Vector up six months ago to help with labor and to give a consistent ration to the cattle. The Vector has given us the option to provide different feed sources to feed the cows that make it easier on us to harvest the feed. Having the option to use different qualities of feed has made it easier to also balance the ration. Since the Vector, we have noticed a positive impact on the health of the cow. We cut our vet bill in half, the cows are breeding sooner, and only see the vet once a month instead of twice. We have little waste of feed and are now able to provide a balanced ration to our heifers. For anyone looking to install a vector, we always encourage to tour many facilities and find the way that will work well for you. When asked if we had to choose between keeping the robots or Vector, we would choose the Vector.
The biggest challenge is maintenance but we do the best we can. We try to keep it kept up so the system works for us for a long time. The service we get from Seehafer’s is great. They answer the phone at all times of the day and show up and do the work. They dig deeper to find problems and correct them until it works properly. If Seehafer’s were here 6 years ago, we wouldn’t have had as many problems.”